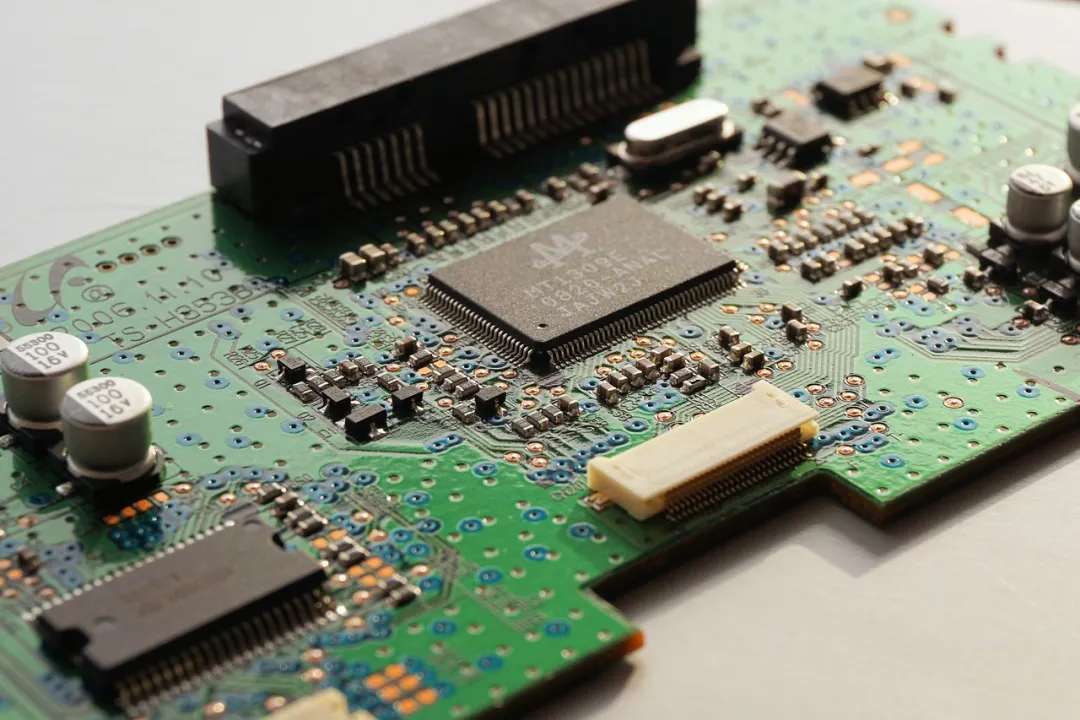
7.电子元器件与FLUX中活性物质反应。
3.PCB阻焊膜质量不好,容易导电。
16.波峰不平。
2.锡不好(如:锡含量太低等)。
3.PCB的问题:如:PCB本身阻焊膜脱落造成短路
2.排风系统不完善
D、PCB贯穿孔不良
10.PCB设计不合理;造成元器件在PCB上的排布不合理,影响了部分元器件的上锡
6.稀释剂添加过多
4.未及时添加稀释剂,造成FLUX浓度过高

干货分享丨5大SMT焊接常见工艺缺陷及解决方法
二去费时费钱。所以本文收集了:在SMT贴片焊接制造中,较为常见的5项工艺缺陷,帮助大家了解SMT贴片工艺,少走弯路,少“翻车...


3D AI工业外观检测系统:提升质量控制与生产效率的关键技术
摄出超过100种缺陷,并首创解决了金属塌边缺陷问题。并可采用调制条纹光检测高反及高透材质的表面缺陷。 2.高敏感度AI检测算法 AI在工业检测中最常见的应用之一是缺陷检测。AI通过...

关于家电产品LED发光二极管引脚不上锡的失效机理研究与分析
的现象(见图1);主要表现为局部,引脚表面有许多(见图2);上锡不饱满异常(见图3)。 图1 样件图片 图2 上锡不良引脚 图3 上锡不良引脚 2 SEM&...

PCBA的一些基本知识!电子小白也能懂!
材料:用于将电子元器件与PCB连接起来,常见的焊接材料有焊锡丝、焊锡球、焊锡膏等。选择合适的焊接材料对保证焊接质量和电路稳定性至关重要。 电路设计:这是PCBA的“灵魂”,它决定了元器件在PCB上的...

PLC压线鼻子的正确接法 PLC程序中要用常开的原因
铝制的接线鼻子。 如果按照形状来分,常见的主要有dt,还有ot,ut等各种型号。如果选择的是dt型号,一般来说比较适用于横截面积比较大的电线,可以采用压接的方式。如果选择的是ot的接线鼻子,适用...


