主机厂都为他们的电动汽车配备了BMS,那为什么还是不能制服电动汽车的火爆脾气,避免或减少冒烟、自燃甚至爆炸事故呢?显而易见,上述BMS是有线连接方式,一旦因汽车恶劣环境而出现线缆连接问题,系统便形同虚设了
近日,比亚迪股份董事长王传福在“2021中国电动汽车百人会论坛”上呼吁,将电池针刺试验纳入国家强制标准……但是,这就可以消除大多数发热自燃的事故隐患吗?另外,主机厂不是都在电动汽车上搭载了BMS(电池管理系统)吗,怎么关键时刻掉链子呢?是像王传福建议所指从电池入手,还是在BMS上做文章,哪个更有普遍意义呢?
为什么发热、冒烟、自燃?
电动汽车自燃的原因很多,但八九不离电池。王传福的“将电池针刺试验纳入国家强制标准,继续完善电动汽车安全法规标准,因为针刺试验是动力电池测试中非常有效、苛刻的一种方法”并没有错,但针刺试验只涉及电池化学类型和电池包设计是否经得起针刺,并没有覆盖电池自燃的更多原因。
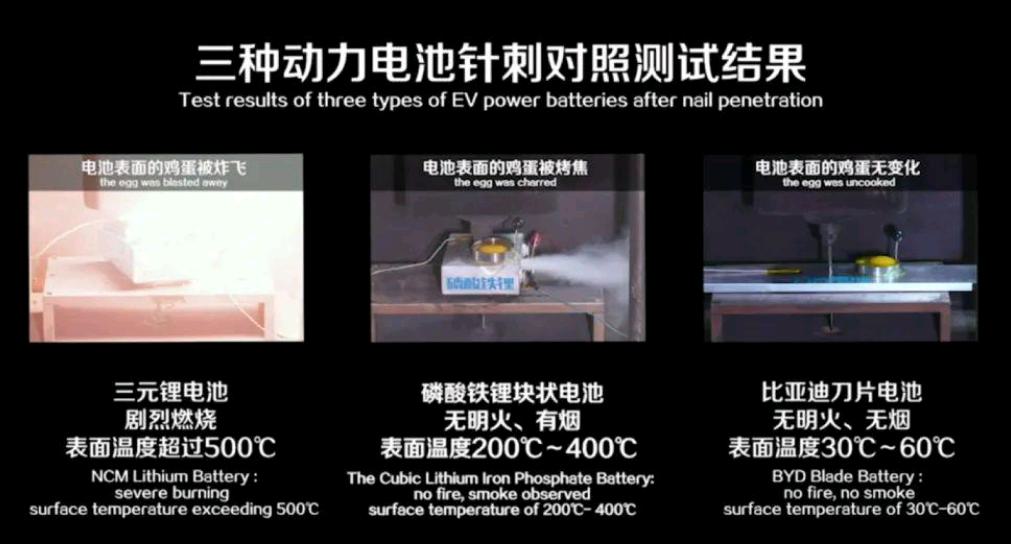
三种动力电池针刺测试结果
问题在于自燃是在什么情况下发生的:
是否电动汽车都是在路上跑着因外力作用所致?车停在那里或是在充电,并没有刺穿,也没有碰撞,也会烧起来。
除了电池本身刺穿,是否还有更多其他因素,如颠簸、碰撞、进水所致电路短路等?
因此,针刺可能有以蠡测海之嫌。
众所周知,燃烧的最重要条件就是温度。夏天高温,纯电动汽车或其他车型都容易发生自燃,因为电池、电路最怕高温,超过温度临界点就会引起局部发热,出现冒烟直至自燃。
可是,在寒冷的冬天,电动汽车自燃事故也不少。虽然外界环境温度很低,但颠簸、碰撞、积水路段行驶、电池电解液泄漏等都可能导致电池正负极或相关线路短路,使局部接触电阻变大产生高温,也就是热失控,引燃周围材料。
在现有电池化学条件下,要从电池本身避免发热自燃还不太可能,磷酸铁锂和三元锂电都有自燃发生,虽然也有厂商称其电池“永不自燃”,能信么?因此,必须利用一些手段来监测和控制电池发热,保证其在正常温度条件下提供电力。
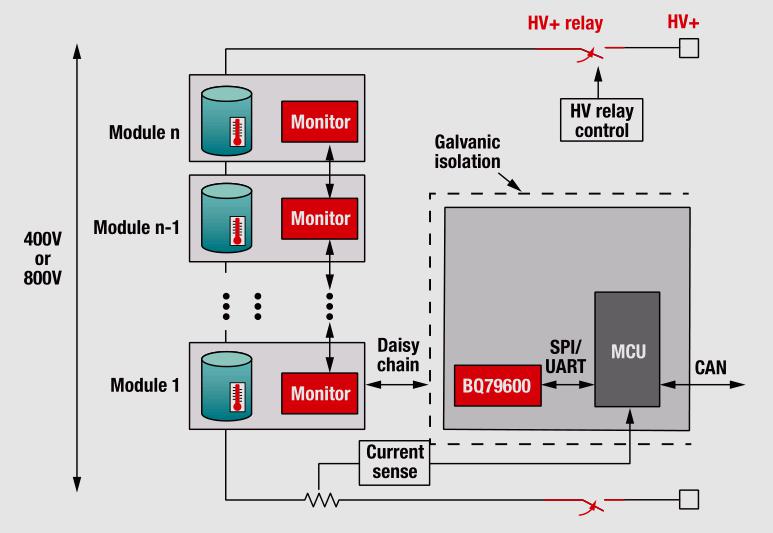
电池监控已成标配
分析表明,目前切实可行的办法还是撇开电池材料乃至电池包设计,从电池使用角度解决如何及时发现电池异常,迅速采取措施的问题。这就是人们熟知的BMS。
不管是什么类型电池,都需要在有限温度和工作电压范围内工作,以获得最佳性能和最安全运行,同时还要防止生产工人、车主、机械师和车辆回收商免受高压和电击,并防止电池穿刺和冲击损伤,避免电池中泄漏或排出液体和气体的影响。
与ICE车辆比,动力电池安全高效工作的温度范围更有限,还要考虑车辆使用或充电中电池组设计的热安全。因此,监测电池电压和温度就成为了动力电池最佳性能和最安全操作的保证。每种类型电池的电压和温度范围都不相同,超出此范围就可能发生不良副反应,从而导致过度自热、内部电气短路,这是级联热失控的第一步,是最大的安全隐患。
为了使电池组保持在安全工作范围,可以使用电池监测ASIC(专用集成电路)来测量电压、温度和电流,并将数据传输到电池控制单元。电池单元电压和温度传感器连接到电池监测ASIC;控制处理器通过读取测量信息来计算电池的当前状态,确保操作在安全范围内进行。对于高压电池组,监控ASIC以堆叠配置排列,每个ASIC并行测量多个单元。命令和数据通过一个隔离通信接口从ASIC传输到ASIC。
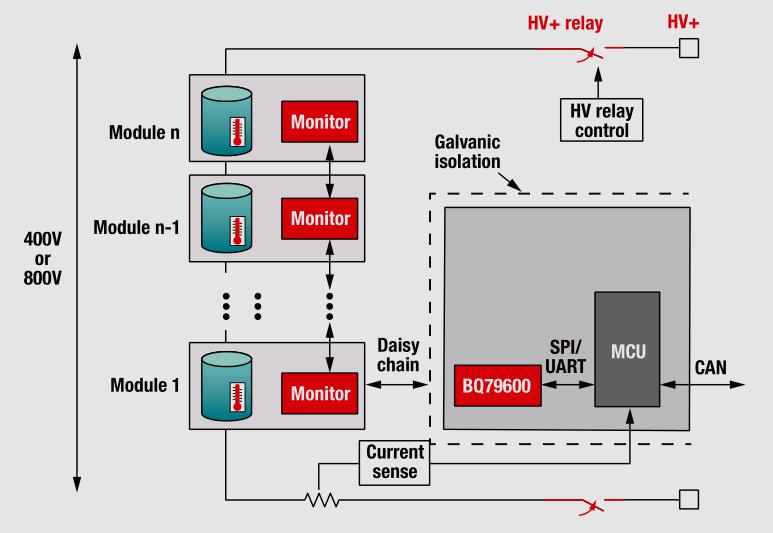
BMS示例
通常,电动乘用车有16、96、128或更多电池单元需要测量;而电动商用车电池单元数可能翻番。电池监控系统中有许多印刷电路板(PCB)、传感器和监控ASIC,这些组件之间的通信连接会因上述原因开路,造成通信中断。这时,电池控制系统法再管理电池组中电池的状态。
BMS的窘境
主机厂都为他们的电动汽车配备了BMS,那为什么还是不能制服电动汽车的火爆脾气,避免或减少冒烟、自燃甚至爆炸事故呢?
显而易见,上述BMS是有线连接方式,一旦因汽车恶劣环境而出现线缆连接问题,系统便形同虚设了。
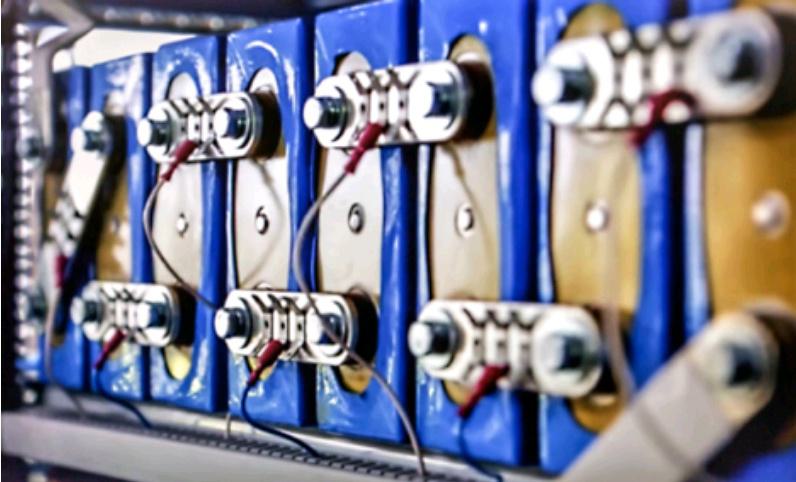
有线连接故障点多
传统BMS面临的挑战包括:
第一,每节电池都必须通过电缆连接一个监视器,布线复杂;
第二,线束和连接器易于出现影响可靠性的故障,需要频繁维护,保修费用较高;
第三,为了使线缆连接更可靠,需要使用粗重的铜线,系统中粗大而笨重的电缆会影响续航能力、组件成本和安全性。
因此,为了实现更高标准的安全要求,必须对电池管理系统进行创新,以实现以下一些新的功能:
用高精度电池监控来确保满足最严格的功能安全标准
用冗余通信协议提供容错性,确保电池组的健康和安全状态
改变连接方式,确保这些监控系统的通信功能万无一失
无线BMS首秀引起轰动
早在2017年3月,当时的凌力尔特(Linear Technology,2019年6月被ADI(Analog Devices)收购)在慕尼黑上海电子展上演示了业界首款无线电池管理系统(WBMS)概念车。公司国际销售副总裁David Quarles、Dust Networks产品总裁Joy Weiss进行了现场发布。
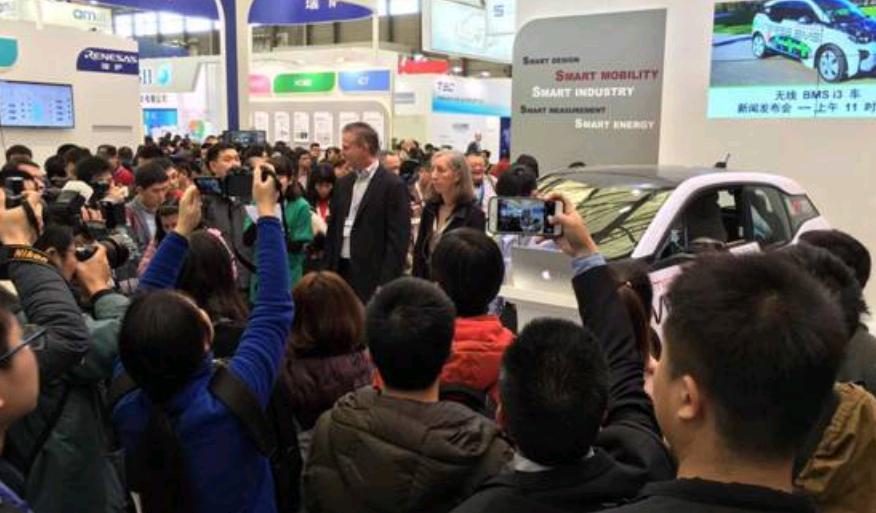
无线BMS概念车引起轰动
David Quarles表示:“无线BMS概念车由设计合作伙伴欧洲电池制造商LION Smart开发,它将凌力尔特高度准确的电池组监视器及SmartMesh® 无线网格网络产品在宝马BMW i3车型上进行了整合,取代了电池组和电池管理系统之间的传统有线连接。BMS的此项重大突破解决了由于汽车线束及电动汽车和混合动力汽车中连接线引起并长期存在的可靠性问题,并简化了BMS设计和制造。”由LION Smart开发的新电池概念叫“LIGHT Battery”,具有模块化、安全和无线特性。
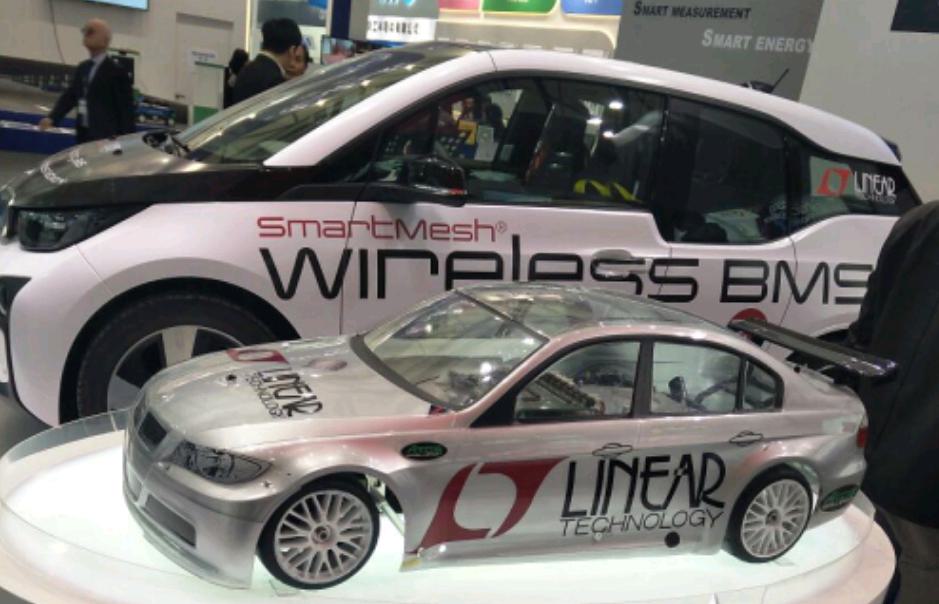
宝马无线BMS概念车
Joy Weiss介绍说,相比有线BMS系统,SmartMesh WBMS具有四个方面的优势:
更安全:SmartMesh采用128位加密的专用网络,利用路径分集和跳频可实现大于99.999%的可靠性,避免导线、连接器破损引起的系统故障
更智能:很容易增加更多传感器,有助于改善SOC(续航里程)和SOH(使用寿命)
更环保:每辆典型车辆可节省10m导线及0.5kg的连接器和变压器,每生产50,000辆车将节省500km导线和25,000kg的连接器和变压器
更便宜:可较低BMS总成本和组装成本,将来的硅片可能比导线和连接器更便宜
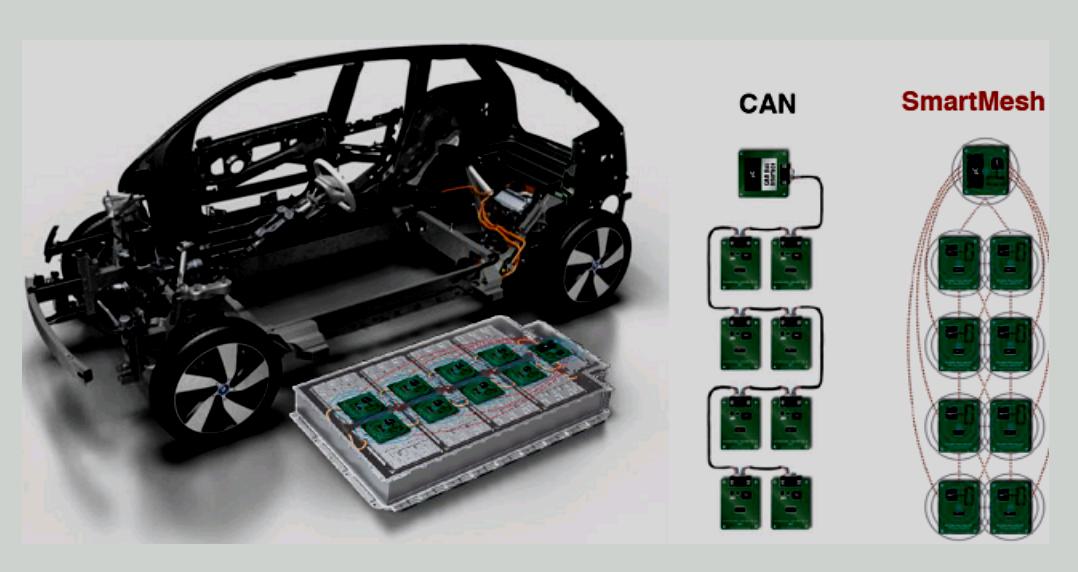
串联的CAN没有SmartMesh WBMS灵活
ADI电池管理系统事业部总经理Herman Eiliya在“2021中国电动汽车百人会论坛”上表示:“BMS是电动汽车动力电池系统的重要组成,它是连接电池与用户之间的纽带。”
据他介绍,与其他竞争技术相比,ADI的5%高精度电池监控技术可以提升10%-15%的电池可用容量和相应行驶里程。“我们能够保证1%的误差。不必像传统BMS需要有人检查电池,无线BMS可以时时刻刻持续监测电池状态,节省人工检测成本。由于整个系统都是无线运行,对于拥有非常丰富产品组合的主机厂益处良多,”他说。
WBMS成硬核,厂商各显神通
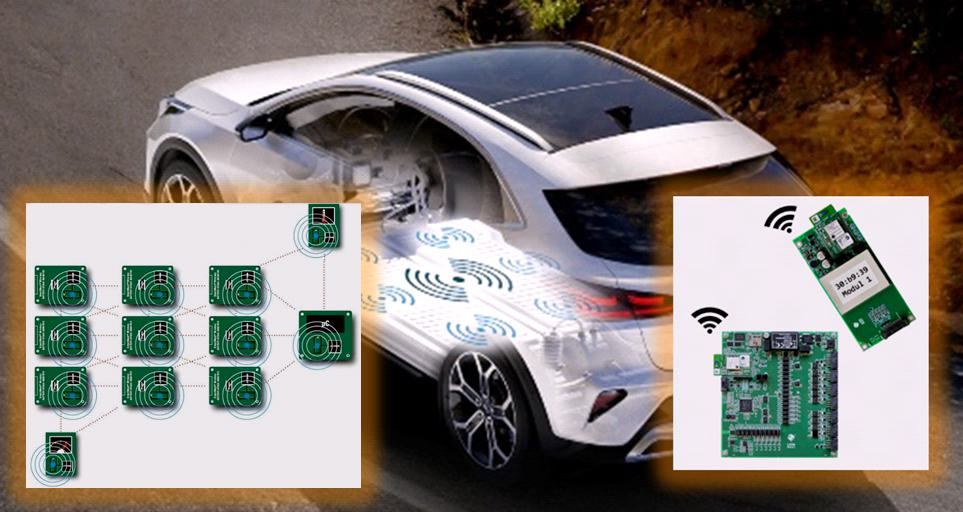
WBMS即将进入量产车
随着电动汽车对轻量化、可靠性、智能化要求的提升,半导体厂商、电池制造商和主机厂都已经意识到:WBMS将是解决传统BMS难题的有效解决方案。剩下来的事情就是看谁有能力从早期研发阶段步入产业化,吃到更大的市场蛋糕了!
蜂巢Sensata布局无线BMS
2019年3月,蜂巢能源与Sensata Technologie签署无线通信BMS合作预研备忘录,加速WBMS产业化进程。双方将深入合作开展无线通信BMS项目,预计将在2021年推出首款量产的无线通信BMS产品。
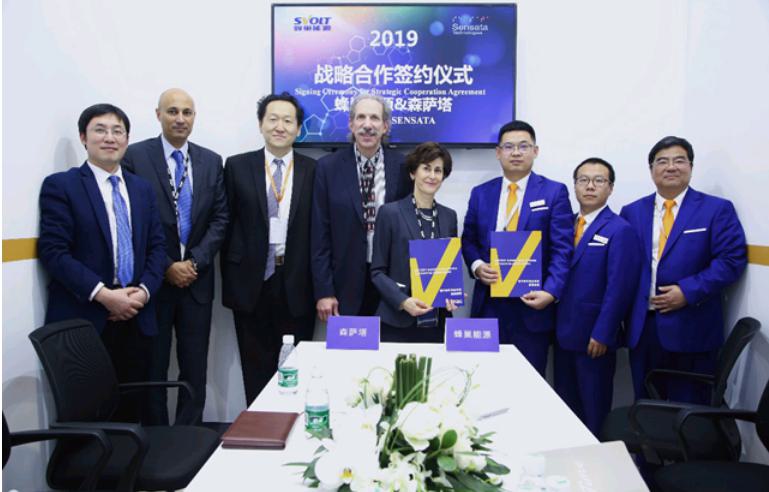
蜂巢能源与Sensata Technologie签署WBMS合作协议
Sensata首席执行官Martha Sullivan认为:“目前BMS常用通信方式包括CAN及菊花链,前者技术成熟,稳定性强,但整体占用空间大,功耗高,成本高;后者虽然成本低,但EMC难度大,可扩展性差。”
他介绍说,与传统BMS传输方式相比,无线通信BMS方式功耗低,可扩展性强,成本适中,同时可减少电池包内线束,简化Pack(电池包)结构,提升整包能量密度,主从板间无高压风险,相比CAN及菊花链更安全,是未来电池管理系统的发展方向。
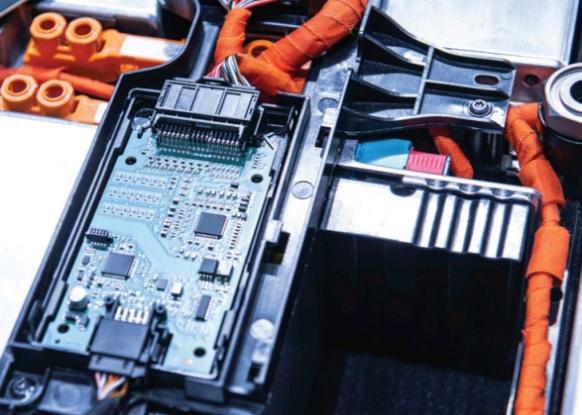
传统BMS存在一些缺点
无论是CAN总线还是isoSPI总线,都是将电池监控芯片串联起来,一旦某处连接出现问题,整个系统都将瘫痪。而无线通信BMS可以减少接插件失效风险:单点失效对整体的影响有限,且在网络中添加和删除新节点也比较灵活。
在电池布局方面,无线连接方案使电池组位置选择更加灵活,同时具备更好的可扩展性,可根据应用需求轻松增加温度、电流等传感器,在恶劣环境中更具备时间同步的优势。
对电池而言,采用无线既减少了低压线束,有助于降低成本和实现轻量化,也降低了电池包复杂度,使模组独立性更强,在系统集成制造、甚至梯次利用上都更为便利。
Maxim无线BMS将易主
2020年初的CES(国际消费类电子展)上,Maxim Integrated(同年7月ADI宣布对其收购)演示了无线BMS,通过取代电池组和BMS模块间的传统有线连接,减轻了电线和连接器重量,消除模块间隔离组件降低了成本、制造复杂性并缩短制造时间,电池组形状也更加灵活。
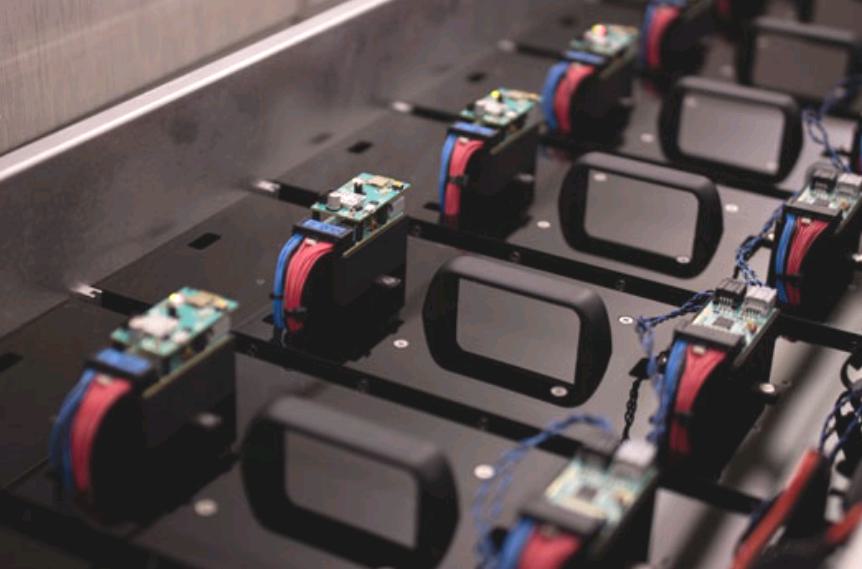
无线(上)和有线(右)BMS配置演示
Maxim Integrated汽车业务部门执行总监Tamer Kira认为:“符合ASIL D(汽车功能安全完整性等级,D为最高级)标准的电池管理解决方案应该能够以一种更高效率和更高安全性的方式来管理电压,从而驱动电动汽车电池组。”
他解释说,符合最高安全级别的BMS有不同架构,基于星型配置的独立CAN架构很稳定,但物料清单(BOM)成本较高,通信速度相对较慢。相比之下,可靠、稳健的菊花链架构能够以更低的成本提供更快、更可靠的通信。
因此,在评估BMS时,需要寻找的另一个有用特性是自动电池平衡,它可以最大限度地减少手动操作(编码等)的工作量。在支持不同的电池组尺寸方面,一定程度的灵活性非常有益。
Maxim独特的BMS技术(MAX17853)是当时业界唯一符合ASIL D标准的电池监测器IC。凭借其独特、专有的菊链式架构和快速SAR ADC,该方案可实现快速、高精度测量,优化混合动力、电动汽车及任何拥有多节串联可充电电池组的系统,提高车辆安全性;在提高锂电池组工作可靠性的同时降低系统成本。
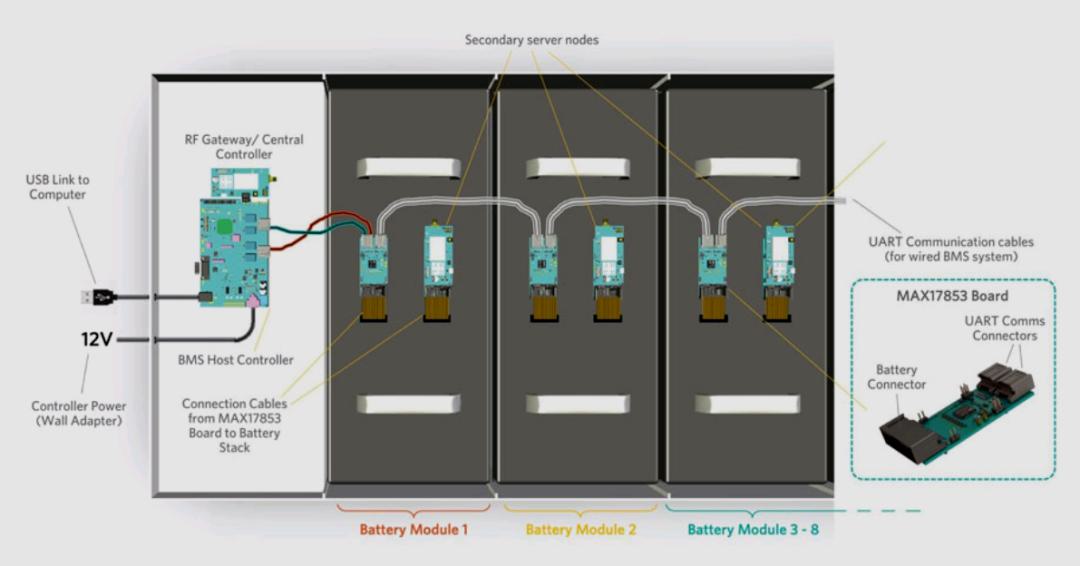
即将易主的Maxim无线BMS
其业界唯一的电容式隔离可以利用电池组上的电容代替昂贵的隔离变压器,将相关BOM成本降低多达90%,并降低故障率(FIT)。
通用汽车和Visteon抢先一步
2020年11月,通用汽车宣布推出首款可量产、完全无线电池管理系统,以持续监控电池组的健康和充电状态。该方案与Visteon及其他技术伙伴合作研发。为此,通用汽车将成为首家在电动汽车中采用WBMS的主机厂。通用将在所有计划中的电动车型Ultium电池中标配该系统。其脚步比BMW更快。
Visteon总裁兼首席执行官Sachin Lawande表示:“我们的无线BMS技术消除了传统系统电池组的线束,为电动汽车提供了一个安全可靠的电池系统。无线创新系统还可以降低终端用户维修成本,因为可能会引发问题的物理设备和电线在新系统中已荡然无存。”
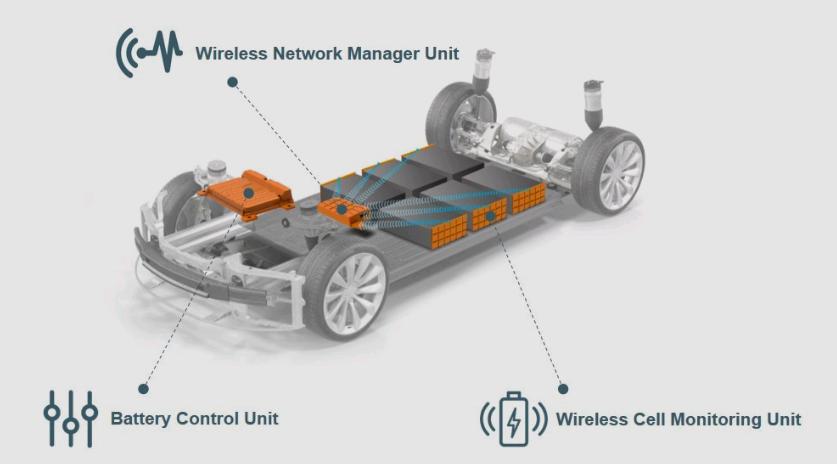
Ultium电池的无线单元
据介绍,该系统提供的平台可在车辆使用寿命内高精度测量电池状况,让每个电芯的能量利用实现最大化,延长车辆续航里程。此外,新型BMS系统也可支持安全可持续性的零钴电池化学,如磷酸铁锂(LFP),主机厂正致力于实现此种可持续性目标。该模块化解决方案支持多种充电协议,满足主机厂在成本、重量和包装方面的要求。
通用汽车希望该无线BMS系统能够推动搭载Ultium电池的电动汽车更快上市,因为研发具体通信系统或为每辆新车重新设计复杂的配线方案并不需要时间。相反,无线系统有助于确保未来通用汽车产品线中Ultium电池的可扩展性,包括不同品牌及重型卡车和高性能车辆等不同车型。
这款方案的技术伙伴就是上面提及的ADI,技术特性不再赘述。
德州仪器紧追不放
今年1月,在以全数字化方式进行的CES 2021上,德州仪器(TI)率先发布了业内首个既通过TÜV SÜD评估,又满足ISO 26262 ASIL D功能安全等级的无线电池管理解决方案。
“2021中国电动汽车百人会论坛”上,TI中国区嵌入式与数字光处理应用技术总监师英表示:“这一解决方案可提供业界最出色的网络可用性,支持跨多平台可靠扩展,有助于汽车客户设计制造更安全、可靠、高效且行驶更远的电动汽车。”
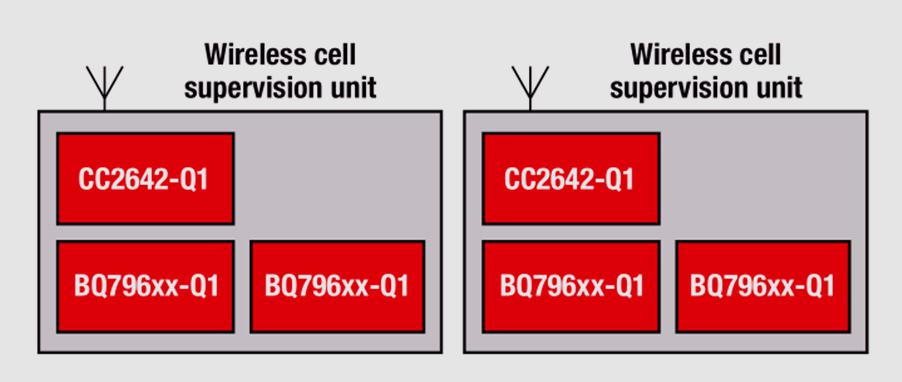
TI无线BMS示例
该无线BMS产品由以下两部分组成:
SimpleLink™ 2.4GHz CC2662R-Q1无线微控制器(MCU):采用符合AEC-Q100标准的Arm® Cortex®-M4,经优化可实现低功耗、扩展温度范围和增强安全性;该器件采用专为无线BMS用例开发的新无线协议,解决了通信错误检测和安全问题。
BQ79616-Q1电池监控平衡器:符合ISO26262功能安全标准,具备通信、温度和电压测量功能芯片级ASIL D等级。借助CC2662R-Q1无线MCU,可以在主机系统处理器与BQ79616-Q1之间进行稳定可靠和可扩展的数据交换。
据介绍,与有线连接相比,该解决方案的无线协议可以实现业界最好的网络可靠性(超过99.999%)和最大300ms的网络重启可用性。其无线协议是基于2.4GHz频段运行的低功耗Bluetooth® 技术编制的专有无线BMS协议。
无线MCU可提供高吞吐量和低延迟的专用时隙,以防止数据丢失或损坏,使多个电池单元能够以±2mV的精度向主MCU发送电压和温度数据,且网络数据包错误率小于10-7。
主机厂可以利用安全驱动工具减少潜在威胁,例如密钥交换和刷新;独特的设备身份验证;调试安全;基于联合测试行动小组(JTAG)协议锁定的软件IP保护;高级加密标准(AES)128位加密加速和消息完整性检查。
考虑到主机厂的长期设计需求,无线BMS创新技术还提供更高的可扩展性。专有协议可提供市场上最高的吞吐量,使主机厂能够在不同电池配置中(如32、48和60个电池单元的系统等)将采用单个无线片上系统的电池模块与多个BQ79616-Q1电池监视器相连。这样的系统设计支持多达100个节点,每个节点都达到业界最低延迟(低于2ms),且每个节点的测量均可实现时间同步。
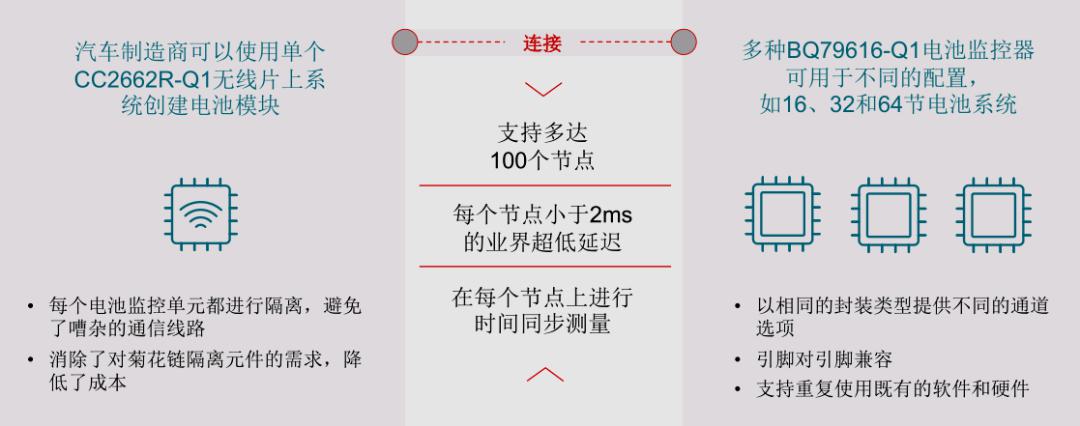
主机厂选择更灵活
也许是和特斯拉掰手腕的机会
“2021中国电动汽车百人会论坛”上半导体公司不过5家,其中两家谈到了无线BMS技术,可见其意义非同小可。不过,目前真正在量产车中采用无线电池监控的好像还没有,开始评估的也是少数。甚至连爱忽悠的马斯克也还没有说无线BMS如何如何。
此前,特斯拉先进的BMS技术是其在市场上脱颖而出的胜负手之一,它一直将其BMS视为最高机密,一直由自己把控。不过,随着几款车型的大量上市,其BMS已了然于天下。我至今仍未发现特斯拉采用无线BMS的蛛丝马迹,除非它的保密工作滴水不漏。其他主机厂,包括传统的和新势力,或许可以在这方面和特斯拉掰掰手腕!
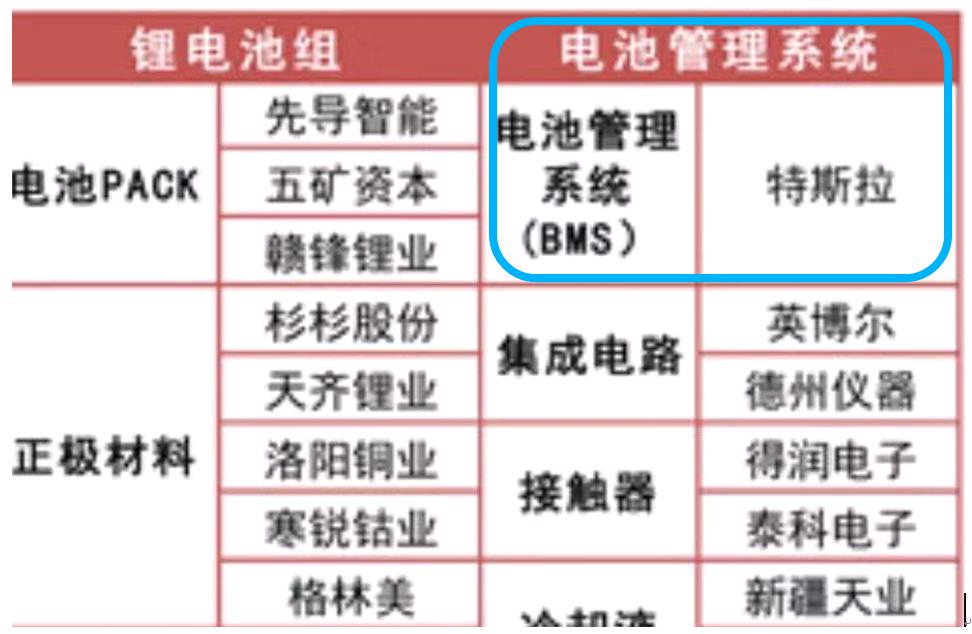
特斯拉产业链之BMS
总之,打造一款更安全、更智能的未来汽车需要的正是无线BMS解决方案所提供的各种优异特性:
确保精确监测和平衡电池电压,提高电动汽车的可靠性和效率,保证电池组和车辆安全运行
集成式硬件架构及系统软件可扩展用于多个汽车平台,主机厂无需对电池模块配置做出大的更改,大幅降低电池组设计成本,并容易与热管理系统和其他车辆控制系统集成
有助于车辆设计师减少繁重、昂贵且需要频繁维护的布线,并减轻汽车重量,延长行驶里程
主机厂可跨量产车型灵活调整设计,更快进入量产阶段