15 Views of Printed Electronics Smart bottles want penny NFC tags
SANTA CLARA, Calif. — Printed, flexible electronics are slowly moving forward on a number of fronts, according to speakers and exhibitors at the annual IDTechEx event.
U.S. and China governments are funding small, separate research efforts that will have prototype production lines running next year. E-textile companies are making in-roads in specialty garments. Printed NFC tags are already being added to a handful of high-end consumer products.
Parker has started shipping a flexible strain sensor, and ST Microelectronics will sample a printed battery before the end of the year. It’s all good progress, but the Holy Grail of mainstream consumer products is still far off.
For example, experts from the Coca-Cola Co. and Unilever said in a panel session that the vision for NFC tags printed on every bottle of soda and detergent is still not practical. The tags could create interactive products that users tap with smartphones to get coupons or other information.
The consumer giants want tags that cost a penny or less, but today, they cost more than an order of magnitude more. The app also requires a lot of education among both marketers and consumers, they said.
“We don’t have a lot of margin, and beverage packaging has to endure travel, stacking, water, heat, and cold,” said Frank Fu, a senior technologist for Coke. With 15 million refrigerated dispensers around the world, the company is “exploring all kinds of possibilities” for reducing costs, increasing interactivity, and tracking assets.
“The consumer company and its tech suppliers both need new business models to enable smart containers,” said John Snow, a packaging manager for Unilever, which sells everything from soap to butter and ice cream. He suggested the consumer giant could think of NFC as part of the cost of an ad, rather than a product, but it has to teach consumers how “a smart bottle can talk to you … [and learn] what we can do with the data to make it valuable.”
“Printed electronics needs a big rain maker,” Snow suggested. “The big issue for us is integration. There are great ideas out there, but great ideas are only one piece of the puzzle — we need to put together all of the pieces to bring the technology to life, so we need a collaborative group.”
“Among other markets, glucose sensors for diabetics make up the majority of today’s $6 billion market for printed sensors,” said Raghu Das, chief executive of IDTechEx (see chart below). But the category is expected to decline as governments put pressure on companies selling for as much as 60 cents the strips that cost two cents to make.
Next page: Printed electronics ramp manufacturing
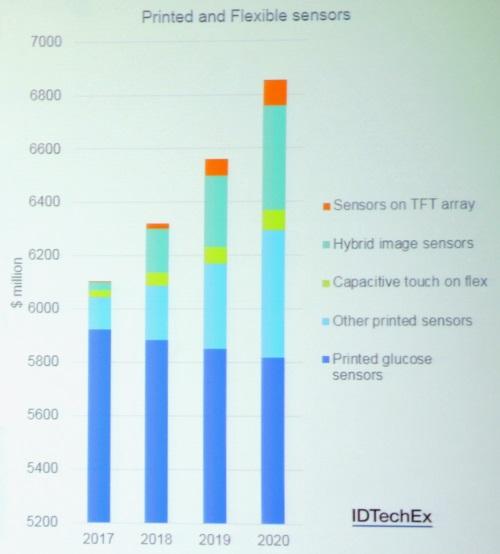
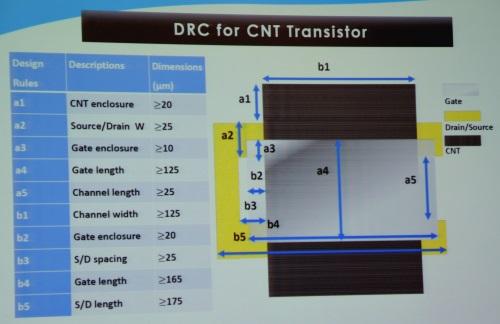
“Manufacturing processes for printed electronics need to get automated,” said Jason Marsh, director of technology for NextFlex, a printed electronics center set up last year with $75 million in U.S. funding. So the center is working with Ansys and Hewlett Packard Enterprise on an 18-month project to deliver EDA tools, starting with a design rule checker for printed circuits (above).
“All of our great products have been hand-walked through production, but you need a level of digital automation,” said Marsh. The first programs should be available by June so “you can model in software if something will work … that allows you to make decisions in real time.”
Today’s printed resistors, transistors, and diodes are not great, but … they are critical for reaching the sub-one-cent NFC tag,” he said.
The center will start putting in equipment early next year for a pilot manufacturing line in San Jose. Meanwhile, it is working on two projects to develop new production tools.
The U.S. is playing catchup with Europe, which has spent several hundreds of millions on existing centers, according to Das of IDTechEx. He also said that China has budgeted $50 million to equip a similar center.
On the show floor, Novacentrix showed its PulseForge 1200 (below). The system uses Xenon lights to shave to a few milliseconds the process of curing flexible electronics, which can take half an hour in a conventional oven. The approach also helps create higher-quality flexible parts with less risk of damage than ovens.
So far, the company has sold six of the $250,000+ systems, many to research outfits. Its rival, Xenon Corp., has systems using similar technology in as many as 100 centers worldwide.
Next page: Niche markets try on e-textiles
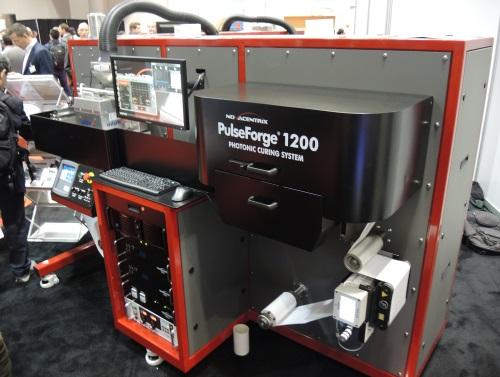
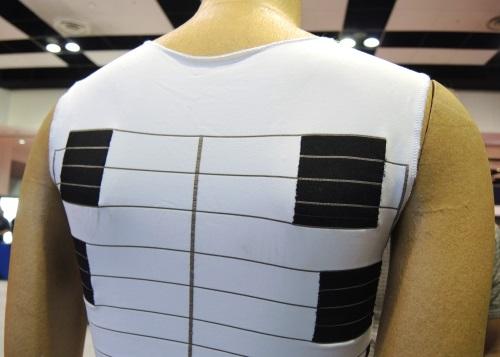
“Ten years ago, we made our own conductive yarns, but we don’t need to today,” said Christian Dalsgaard, founder and chief technologist of Ohmatex, a Danish company that spun out of an e-textile research project in Europe.
The company’s Embrace shirt (above) links six carbon-fiber pressure sensors using a third-party conductive yarn made with spray-on copper. So far, the shirt, used to measure the tightness of braces worn by teens with scoliosis, has withstood 129 washes.
The company, which acts as a systems integrator, also developed a shirt to measure muscle activity for astronauts. It is currently used in training programs but may be worn on the International Space Station in the next year or two.
Ohmatex works with half a dozen vendors of conductive yarns. It also makes a variety of its own electronic buses for e-textiles, some using copper wire (below).
Next page: STM preps a printed battery for IoT
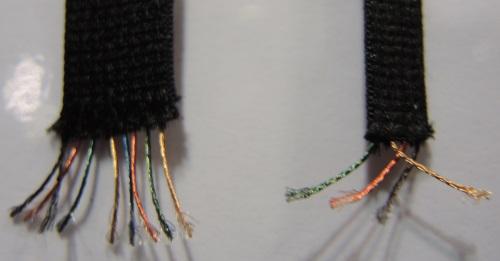
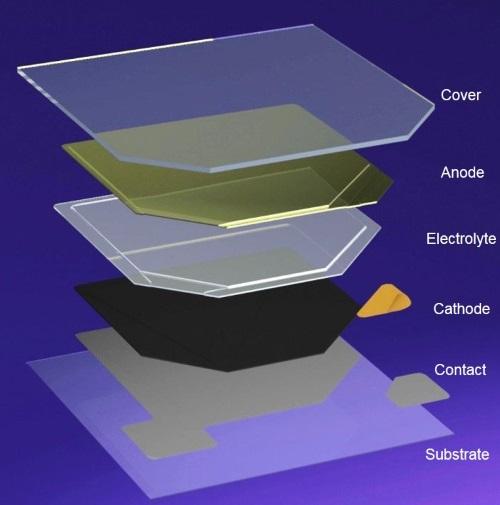
STMicroelectronics described a printed, rechargeable thin-film battery (above) that it expects to sample before the end of the year for uses ranging from hearing aids and implants to IoT sensors in smart cities, cars, and transportation systems.
An emerging class of batteries use printing techniques to deliver low-density products that could be alternatives to supercapacitors, according to Andy Keates, a principal battery engineer from Intel who spoke at the event. The batteries are ideal for IoT nodes, especially if they can withstand reflow temperatures and be shaped and soldered to printed circuit boards, he said.
The ST battery is made in a plant in Tours, France, by sputtering anode, cathode, and electrode layers that work together while in a solid form. The 3.9-V device is suitable for thousands of cycles and can get 80% of a charge in 30 minutes. ST developed a way to charge the batteries from a smartphone via NFC.
The battery currently provides about a milliamp-hour of energy but has potential to reach 300 mAh eventually. ST’s road map (below) shows it delivering 2.5x as much early next year. A version of the technology available in custom sizes could hold up to 10 times more energy.
ST created tools to simulate the battery’s flat discharge cycle as an aid for system designers. It has a separate tool for designing versions of the battery in custom shapes.
Separately, ST is participating with 35 other companies in a European research program that aims to pave a path by 2020 to batteries for smart objects offering more than 20 mAh and 300 Wh/liter energy density.
Next page: Stretchable sensor reaches the market
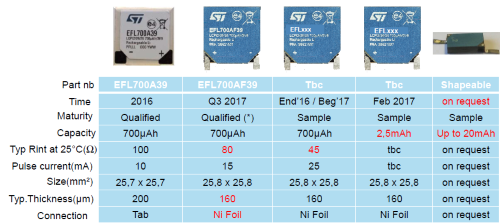
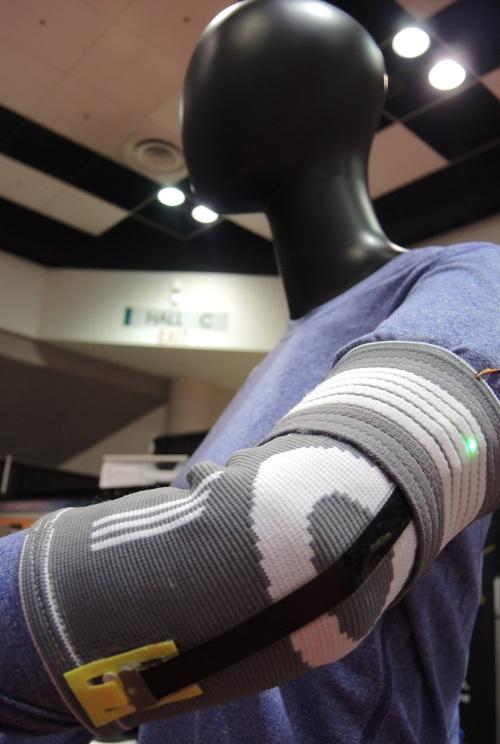
Parker Hannifin demoed a stretchable strain gauge (above) that it started selling in October. The current version provides a 50-micron resolution over a 100% stretch. Engineers are working to eliminate noise in oscillator circuits to deliver in a few months a version with resolution of less than two microns.
The sensors will be used for a wide range of industrial IoT applications, such as checking tension in robotic grippers, vibration in motors, and expansion in tubes.
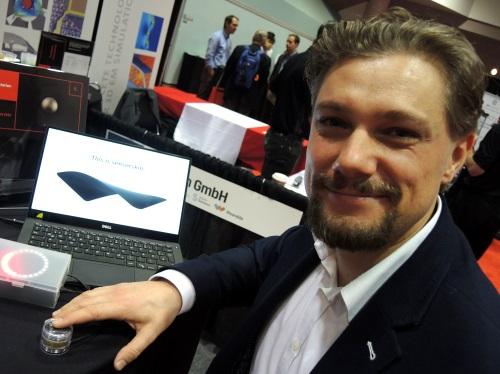
While working at a German aerospace research institute, Michael Strohmayr (above) developed a novel touch sensor. Created as part of a project to give robots a sense of touch, the conformal sensor provides a 1.5-mm spatial resolution. That’s enough for a robot to distinguish whether it’s holding a cube or a sphere.
Now Strohmayr’s company, Tacterion (Munich), is seeking commercial markets for the sensor in areas ranging from gaming to the industrial IoT. Part of the innovation was in an additive manufacturing process to build the sensor. Another part was placing the sensor just below the upper surface of the flexible material.
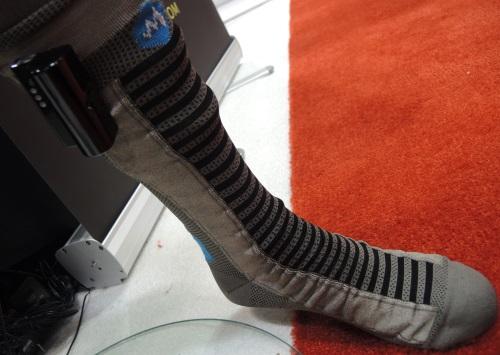
Like Denmark’s Ohmatex, Canada’s Myart acts as a system integrator, making wearable products using its automated production facility and expertise in conductive yarns to add heat, light, and sensing to fabrics. Its heated socks (above), based on woven electronics, were one of half a dozen products it showed.
Wearables need a wide range of conductive yarns because different heat, light, and sensor apps require different amounts of electricity. The company uses a range of third-party conductive yarns today, but it plans to develop its own soon, implanting silver nanoparticles in yarns in ways it hopes will better withstand the washing machine.
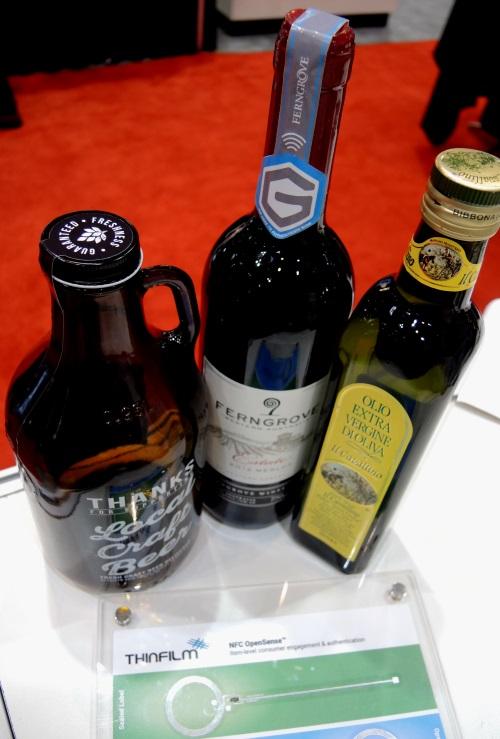
Thin Film Electronics ASA (Oslo) recently opened a plant in San Jose, where it is making NFC devices based on a novel technique for printing on a steel substrate. It prints a few hundred transistors and discretes to create a read-only NFC circuit that transmits a tamper-resistant code to generate a URL on a smartphone. A handful of high-end consumer products are already using the tags, which cost less than a dollar.
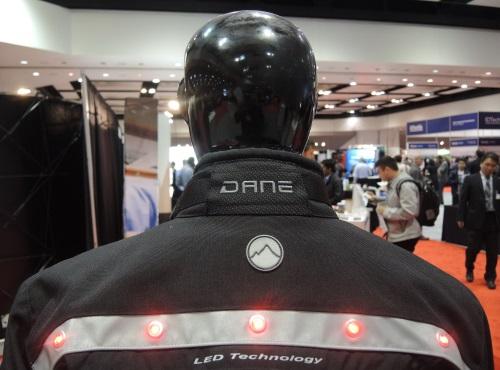
A high-end Dane motorbike jacket with safety LEDs integrated in the front and back by Interactive Wear of Germany was on display (above). Nearby, researchers at North Carolina State University showed an ECG dress with LEDs (below).
Next page: Embroidering with LEDs
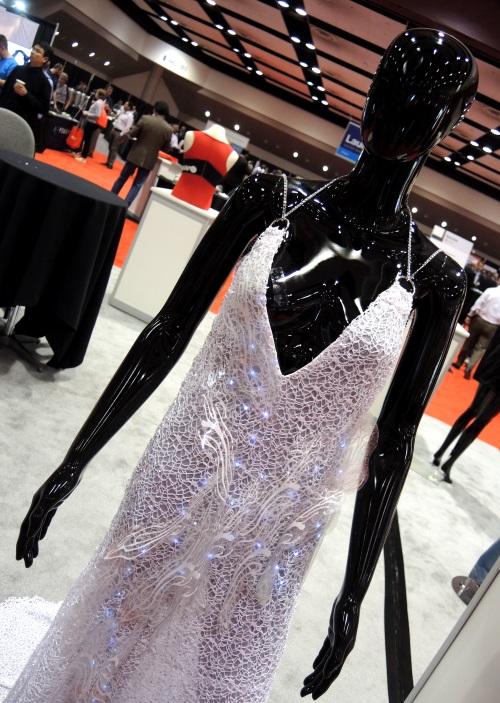
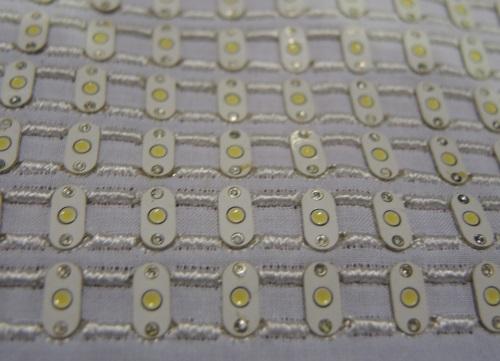
Forster Rohner of Switzerland has created a novel way of mounting LEDs in a kind of embroidery (above) for use with clothing, though not integrated into fabrics directly. The company also provides help integrating sensors and heating elements into clothing.
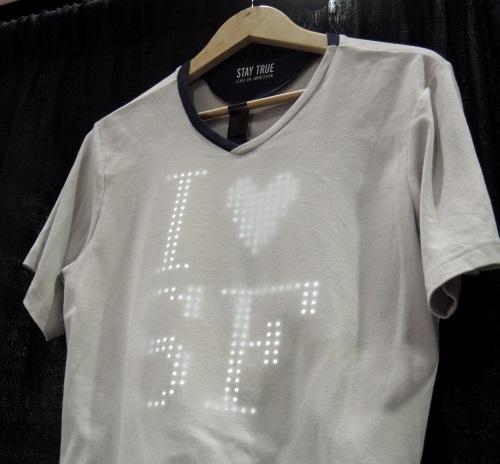
— Rick Merritt, Silicon Valley Bureau Chief, EE Times
相关文章
专栏
-
- 半导体行业观察
-
- 摩尔芯闻
最新新闻
热门文章
- 1
- 2
- 3
- 4
- 5
- 1
- 2
- 3
- 4
- 5
- 1
- 2
- 3
- 4
- 5